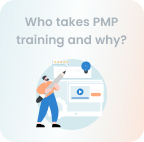
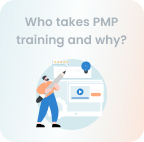
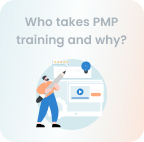
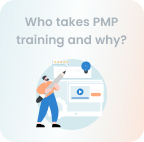
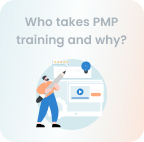
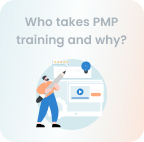
26 September 2024
Veronica Davis
Have you ever wondered how project managers keep things on track and avoid unexpected pitfalls? The secret often lies in the Control Chart in PMP. These powerful tools help monitor project performance by analyzing variations and trends. This blog reveals how Control Charts can transform your project management strategy. Let’s explore what it is all about.
Table of Contents
1) What is a Control Chart in PMP?
2) A Brief History of Control Charts
3) Key Components of a Control Chart
4) Different Types of Control Charts
5) The Importance of Control Charts in PMP
6) How to Create a Control Chart?
7) Advantages of Using Control Charts
8) Challenges in Using Control Charts
9) Examples of Control Charts
10) Conclusion
A Control Chart in Project Management Professional (PMP) is a powerful graphical tool used to monitor the stability of processes over time. It visually represents performance metrics and helps project managers track process variations to determine whether they fall within predefined limits, known as control limits. These charts typically include a central line for the mean, an upper control limit, and a lower control limit.
Control Charts are especially useful in quality management, enabling teams to identify trends, patterns, or anomalies. By proactively monitoring these variations, project managers can intervene early to prevent defects, reduce waste, and maintain consistent project performance. Control Charts are crucial for ensuring process efficiency, maintaining quality standards, and keeping projects aligned with their goals.
Walter A. Shewhart, a physicist and statistician at Bell Laboratories, introduced Control Charts in the 1920s as a groundbreaking tool for improving manufacturing quality control. Before Shewhart’s innovation, quality control largely relied on reactive and costly inspection methods.
His revolutionary idea was to use statistical methods to monitor processes, enabling companies to identify and address variations before they led to defects. This shift from reactive to proactive quality management marked the beginning of modern statistical process control (SPC).
Shewhart’s Control Charts provided a way to distinguish between common cause variations (natural fluctuations) and particular cause variations (abnormal, out-of-control factors), making them invaluable for maintaining consistent production quality.
Over time, Control Charts transcended manufacturing and were adapted across various industries, including healthcare, finance, and project management. In project management, they help ensure process stability, allowing teams to monitor performance metrics, control risks, and improve project outcomes through data-driven decision-making.
A Control Chart typically consists of several key components:
1) Data Points: Represent actual performance data collected over time.
2) Control Limits: Upper and lower thresholds that define acceptable variations.
3) Central Line: The average or mean value of the data points.
4) Control Lines: Horizontal lines indicating the control limits.
5) Outliers: Data points that fall outside the control limits, signalling potential issues.
These components work together to provide a clear picture of process performance and highlight areas needing attention.
Control Charts come in various types, each suited for specific kinds of data and processes:
1) X-bar and R Charts: Used for monitoring the mean and range of variables.
2) P Charts: Used for monitoring the proportion of flawed items in a process.
3) C Charts: Track the number of defects per unit of measurement.
4) U Charts: Monitor the number of defects per output unit, accounting for varying sample sizes.
Choosing the proper Control Chart type depends on the data's nature and the monitoring process.
Control Charts are vital in project management because they ensure that processes remain stable, efficient, and within control limits. By giving a visual representation of performance metrics over time, these charts help project managers detect trends, variations, or deviations early. This allows for timely intervention, preventing minor issues from escalating into major problems that could derail the project.
The real-time monitoring of processes using Control Charts enables project teams to make data-driven decisions, enhancing process control and risk management. Additionally, Control Charts promote continuous improvement by highlighting areas that need refinement, ensuring that quality standards are consistently met throughout the project lifecycle. They are critical tools for maintaining efficiency, minimizing defects, and optimizing project outcomes.
Creating a Control Chart involves several steps:
1) Collect Data: Gather performance data over a defined period.
2) Calculate Averages: Determine the mean of the collected data.
3) Determine Control Limits: Establish upper and lower control limits based on the data’s variability.
4) Plot Data Points: Chart the data points, control limits, and central line.
5) Analyze Trends: Examine the chart for trends or deviations from the control limits.
Following these steps ensures that the Control Chart accurately reflects process performance and highlights improvement areas.
Control Charts offer numerous benefits:
1) Early Detection: They help identify problems before they become significant issues.
2) Process Improvement: By highlighting variations, Control Charts guide efforts to enhance process efficiency.
3) Data-Driven Decisions: Provide objective data to support decision-making and process adjustments.
4) Consistency: Ensure processes remain stable and within acceptable limits over time.
These advantages make Control Charts an invaluable tool in project management for maintaining high quality and performance standards.
Despite their benefits, Control Charts come with challenges:
1) Data Quality: Accurate Control Charts require high-quality, consistent data.
2) Complexity: Interpreting Control Charts can be complex, especially for beginners.
3) Resource Intensive: Creating and maintaining Control Charts can require significant time and resources.
4) Over-Reliance: Relying solely on Control Charts without considering other factors can lead to misinterpretation.
Addressing these challenges involves careful planning, training, and integrating Control Charts with other project management tools and techniques.
Here are a few examples of how Control Charts are applied:
1) Manufacturing: Tracking the number of defects per batch to ensure quality standards.
2) Software Development: Monitoring bug rates during different phases of a project.
3) Customer Service: Measuring response times to customer inquiries and identifying trends.
These examples illustrate how Control Charts can be adapted to various industries and processes, providing valuable insights and enhancing overall performance.
Mastering the Control Chart in PMP is a game-changer for project managers. By effectively monitoring and analyzing process performance, you can make sure that your projects stay on track and meet their goals. Embrace the power of Control Charts to drive continuous improvement and achieve project success.
© Copyright 2017. All rights reserved. Contact: PMP® TRAINING ACADEMY.